(2) Tuberculosis
Tubeless conversion means that the inner tube is not assembled in the inner cavity of the tire, and the airtightness is maintained by the tightness between the inner liner on the inner side of the outer tube and the bead and the spoke. When such a tire is pierced, the eyelet is compressed by the elasticity of the tire material to prevent leakage. Tubeless tires also save the pad
Belt, which simplifies the structure of the tire. Tubeless tires are safe to drive, have low heat generation, light weight, convenient loading and unloading, and long service life. The tubeless structure was first used in military vehicles in the Second World War. It was promoted after the war. At present, it is mainly based on cars, and engineering vehicles and transport trucks are also partially used.
(3) Flattening
Flattening is a new trend that has developed over the past 20 years and is also a trend in the size of tire sections. Taking the ratio of the height/width (unchanged) of the tire section as a parameter, the traditional ratio in the past is 80 or 82 to 100, which is abbreviated as 80 or 82 series. Due to the flattening, it is gradually developed to 70, 60, 55, 50 or even 35. Super flat series.
The tire cross-height H is half the difference between the outer diameter and the radius of the contact after the tire is inflated; and the cross-sectional width B is the maximum distance from the left side to the right side of the bead after inflation. Their ratio B/H (the so-called cross-sectional ratio) is an important structural parameter of the tire. Since the 1950s and 1960s, the trend has changed from big to small.
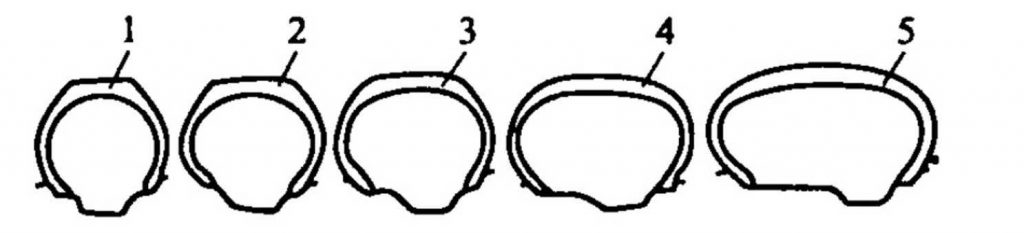
Variations in cross-sectional shape of 88, 82, 70, 60 and 50 series tires
Therefore, flattening means that while the outer diameter of the tire is small, the tire width is relaxed, and as a result, the landing area is increased and the center of gravity of the vehicle is lowered, resulting in improved running stability, which is for the speed of the vehicle. Improvement, high-speed driving safety and improvement in ride comfort are very beneficial, so it is the most important priority in car tires.
(4)Environmentally friendly tire
As the name implies, “Green Tire” is a new type of tire that meets the requirements of the ecological environment. It was first created and named by the French Michelin Tire Company in the 1990s.
The design requirements for tire products are energy efficient and fuel efficient, as energy savings can result in reduced fuel consumption. In other words, under the condition of the same mileage, the green tires are less fuel-efficient than ordinary tires, and the exhaust gas from the automobile and the pollution to the atmosphere are also reduced.
As we all know, the factors that usually affect the rolling resistance of tires come from three aspects: first, the structural parameters of the tire itself, such as flatness, pattern depth, etc.; second, driving conditions, such as vehicle speed, load and inflation pressure; third, road conditions. Green tires introduce a fourth factor, the formulation of the tread rubber.
In the tread rubber formula, in order to obtain excellent mechanical properties, 50 to 60 parts (based on 100 parts of raw rubber) are usually blended with super abrasion resistant or high abrasion resistant carbon black. Such hard carbon black generates severe internal friction during driving, resulting in high hysteresis, high heat generation, and large rolling resistance. Improvement measures are:
First, the precipitated white carbon black is used to replace the partially super-abrasive carbon black, and the substitution amount is 12-15 parts, which is equivalent to 20%~25% of the original carbon black amount;
Secondly, the silane coupling agent Si69 is added to modify the white carbon black, so that the black and white reinforcing agents are uniformly dispersed after being blended, and the combination is good, not only has a superposition effect on performance, but also improves performance. It also reduces the rolling resistance of the tire by 20%~30 3⁄8.
Since carbon black and silica are both nanoscale materials, the product of this new technology is called “biphasic nanofiller”. Infrared spectroscopy analysis was also carried out on the tread rubber using biphasic nanofiller. In addition to the absorption peaks of carbon black and white carbon black, the biphasic superposition absorption peak appeared in the spectrum, which proved the objective existence of the superposition effect.